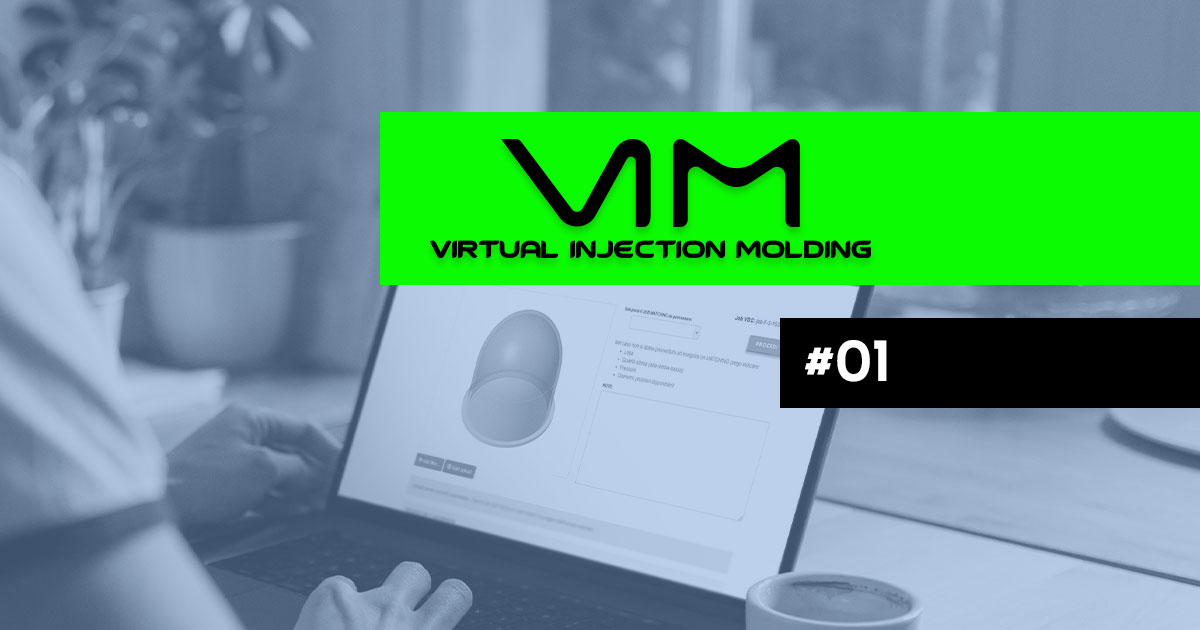
In che modo l'analisi VIM aiuta a prevenire e risolvere problemi: il case study.
Quali sono i vantaggi e i benefici di utilizzare la simulazione virtuale VIM nel caso dello stampaggio di una lente? Scopri la case study, leggi la news!
Vediamo un esempio in cui l'analisi VIM può aiutare nella risoluzione di un problema esistente oppure consentirci addirittura di evitarlo.
Problema
dobbiamo stampare ad iniezione la seguente 'lente' in policarbonato trasparente V0.
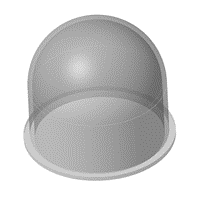
E' una lente per telecamere e quindi non possiamo mettere il punto di iniezione sulla bombatura dove darebbe origine ad un riempimento a 'pioggia' uniforme e senza intrappolamenti di aria ma solo sull'esterno e possibilmente in prossimità della base.
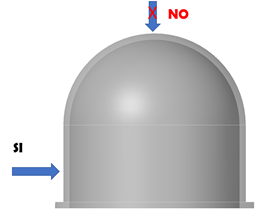
Questo layout di iniezione pone un problema, nonostante la semplicità geometrica dell'oggetto da stampare: il materiale durante il riempimento gira attorno al pezzo prima di completare la cupola portando così il punto di riempimento all'interno del pezzo con conseguente bruciatura.
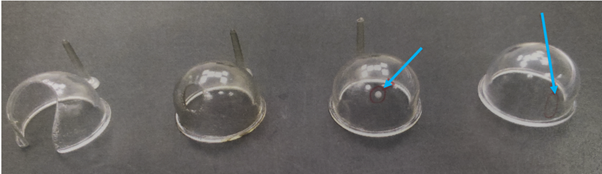
Infatti, dalla simulazione VIM, si evidenzia chiusura del flusso e intrappolamenti di aria:
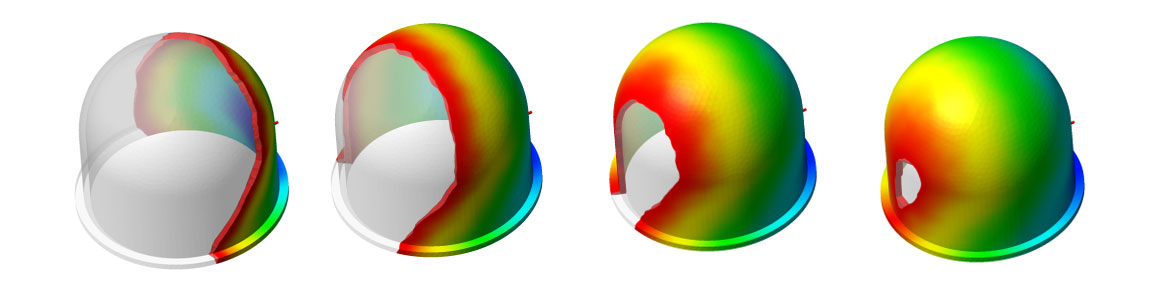
Le considerazioni dell'analisi
Per superare il problema e forzare la chiusura del flusso sulla periferia del pezzo, non potendo spostare il punto di iniezione, l'unica soluzione è lavorare sugli spessori in modo da dare una maggior prevalenza alla zona della cupola rispetto alla zona alla base.
Dopotutto, dobbiamo ricordarci che durante il riempimento valgono le leggi della fluidodinamica per cui il materiale, come qualsiasi liquido, preferisce passare dove fa meno fatica ovvero dove la sezione è maggiore.
Pertanto, dovendo favorire il riempimento sulla cupola diamo spessore a questa zona.
Le soluzioni VIM e la risoluzione del problema con la nostra analisi.
A questo punto la domanda è: quanto spessore dobbiamo dare per ottenere l'effetto desiderato?
Possiamo procedere in due modi:
- Proviamo ad aumentare lo spessore sullo stampo un po' alla volta provando di volta in volta fino ad ottenere l'effetto desiderato. Teniamo conto che lo stampo è lucidato a specchio, quindi ogni intervento richiede la successiva lucidatura delle superfici lavorate
- Usiamo VIM e modelliamo 2-3 soluzioni. Ad esempio, facciamo 0.2, 0.4 e 0.6mm di spessore aggiuntivo sulla cupola.
Ebbene la soluzione con 0.4 mm aggiuntivi è sufficiente a spostare la chiusura del flusso sulla periferia del pezzo.
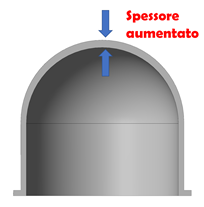
Riempimento con la modifica.
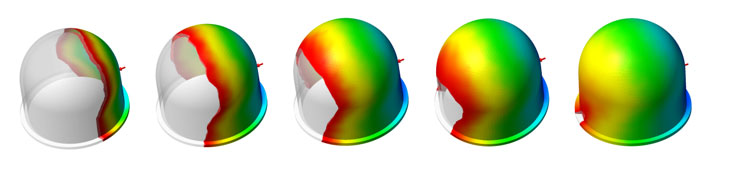
Quindi, attraverso l'uso di VIM abbiamo risolto il nostro problema con un evidente risparmio di tempo e denaro.
Tutti i vantaggi nell'utilizzare l'analisi VIM
Facciamo un confronto ipotizzando un paio di riprese per ottenere il risultato desiderato su di uno stampo mono impronta:
Trial and error |
VIM |
---|---|
2 prove fisiche | 2 analisi VIM (lanciate contemporaneamente con risultato in 24h) |
10 ore di lavorazione stampo | 5 ore di lavorazione stampo |
2 campionature stampo | 1 campionatura stampo |
E' evidente che abbiamo dimezzato i tempi e costi di intervento spendendo solo per un paio di analisi VIM. Se abbiamo attivato un pacchetto stiamo parlando di poche centinaia di euro!
Ovviamente se tutto questo fosse stato fatto a monte e avessimo, come sarebbe ragionevole, considerato nel workflow di progettazione di un nuovo stampo un paio di analisi VIM, il problema non ci sarebbe nemmeno stato perché da subito sarebbe stata evidenziata la problematica cui saremmo incorsi.