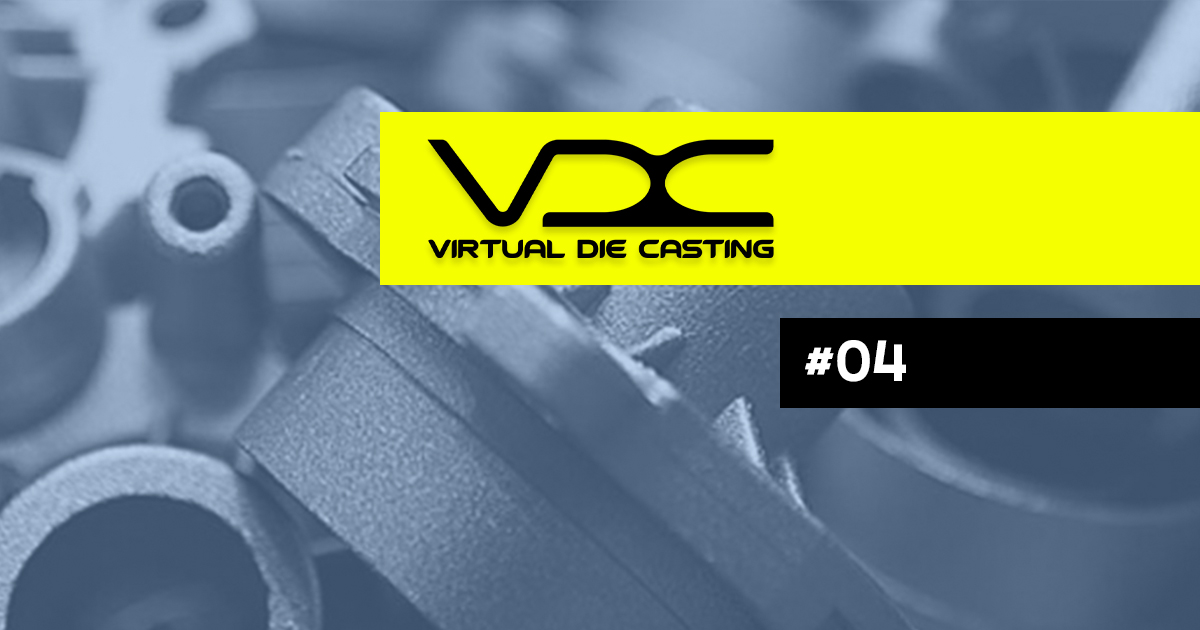
La tecnica DOE nel mondo HPDC: simulazione e realtà
Presentazione dell’analisi DOE per stampo HPDC, o quasi.
Sempre più si parla di Design of Experiments, DOE, o ottimizzazione, nell’ambito dei software di simulazione di riempimento cavità stampo.
Vengono fatte una serie di simulazioni, quindi processi virtuali, variando alcune grandezze (dimensioni e/o posizione gate, velocità, temperatura, pressione, curva di iniezione…), impostando precisi obiettivi (ad esempio minima porosità, max qualità superficiale…) e lanciando una serie di simulazioni incrociate per ottenere l’ottimizzazione delle grandezze in input.
Fantastico!
Ma è questa l’analisi DOE per uno stampo HPDC? Molti credono di si.
Io credo di no, o quantomeno, non solo!
Il metodo DOE: da appannaggio per specialisti all’uso pratico.
Il metodo Design of Experiments (DOE) è diventato una delle tecniche statistiche per la progettazione degli esperimenti più note degli anni ’90.
Il DOE è stato inventato nel 1920 dallo scienziato inglese R. A. Fisher come metodo per massimizzare le informazioni derivanti da dati sperimentali.
Tale metodo si è evoluto nei successivi 70 anni, ma molti sviluppi si sono rivelati eccessivamente complessi dal punto di vista matematico, e quindi esclusivo appannaggio di specialisti.
La relativamente recente diffusione del DOE è attribuita agli studi di Taguchi, ingegnere giapponese che si focalizzò sull’uso pratico anziché sulla teoria matematica di questa tecnica.
Parliamo di esperimenti, quindi parliamo di realtà. Dobbiamo perciò realizzare una serie di esperimenti reali su cui condurre la nostra analisi. Un software non è realtà: è aderente quanto si voglia alla realtà ma è comunque inevitabilmente diverso.
Il metodo di sperimentazione tradizionale.
Ma ora, torniamo alla sperimentazione.
La sperimentazione può apportare valore aggiunto se pensata non solo come conferma di quanto previsto ma anche come potenziale fonte di opportunità di miglioramento non intuibili a priori.
Il metodo di sperimentazione tradizionale si basa sul seguente loop:
- Sviluppo di un’ipotesi teorica;
- Prova-confutazione dell’ipotesi;
- Analisi dei risultati ottenuti;
- Individuazione delle correzioni;
- Effettuazione di ulteriori prove.
Il ciclo si conclude con il raggiungimento di un risultato ritenuto adeguato e se le informazioni teoriche possedute sono stabili e complete, l’approccio è rapido e soddisfacente.
Cosa succede, però, nei processi industriali?
Per processi industriali quali la presso colata o lo stampaggio ad iniezione di termoplastici (che conosciamo bene e direttamente) nessuno vede cosa succede dentro lo stampo.
La complessità dei fenomeni così come il numero delle variabili in gioco è tale da impedirci nella realtà il pieno controllo dei fattori che stiamo indagando.
A ciò si aggiunga che non abbiamo una conoscenza teorica completa del processo affrontato, non conosciamo cioè la relazione di causa-effetto tra i fattori che influiscono sul processo in esame e le variabili da ottimizzare.
Il metodo DOE.
Il metodo DOE consta quindi di due fasi principali:
- Fase 1: screening, identificazione dei fattori significativi e loro correlazione;
- Fase 2: ottimizzazione, identificazione della risposta.
DOE: Fase 1
Occorre effettuare una serie di prove sistematiche per individuare i fattori significativi e la correlazione tra questi. Procediamo nel modo seguente:
- Identifichiamo la/le variabili da ottimizzare, ovvero la risposta che qualifica il processo;
- Distinguiamo i fattori che potrebbero influire sulla risposta;
- Per ogni fattore stimiamo il campo di variabilità ragionevole in relazione al processo di interesse (individuarne il range di variabilità);
- Predisponiamo il piano di prova;
- Eseguiamo le prove;
- Analizziamo i risultati per valutare quali siano i fattori che, singolarmente, influenzano il processo.
Se, ad esempio, consideriamo un numero n di fattori e per ogni fattore individuiamo il valore più alto ed il valore più basso che esso può assumere, effettueremo tante prove quante sono le combinazioni possibili tra i fattori, ovvero 2^n prove.
Infine occorre confrontare tra loro gli effetti dei singoli fattori per individuare in che misura ognuno influisca sul processo.
DOE: Fase 2
La fase 2 della tecnica DOE prevede a questo punto la capacità di estrapolare una formulazione matematica (una funzione n-dimensionale del nostro processo) della risposta del sistema, in funzione delle variabili, al fine di individuare la condizione di ottimo e valutarne la stabilità.
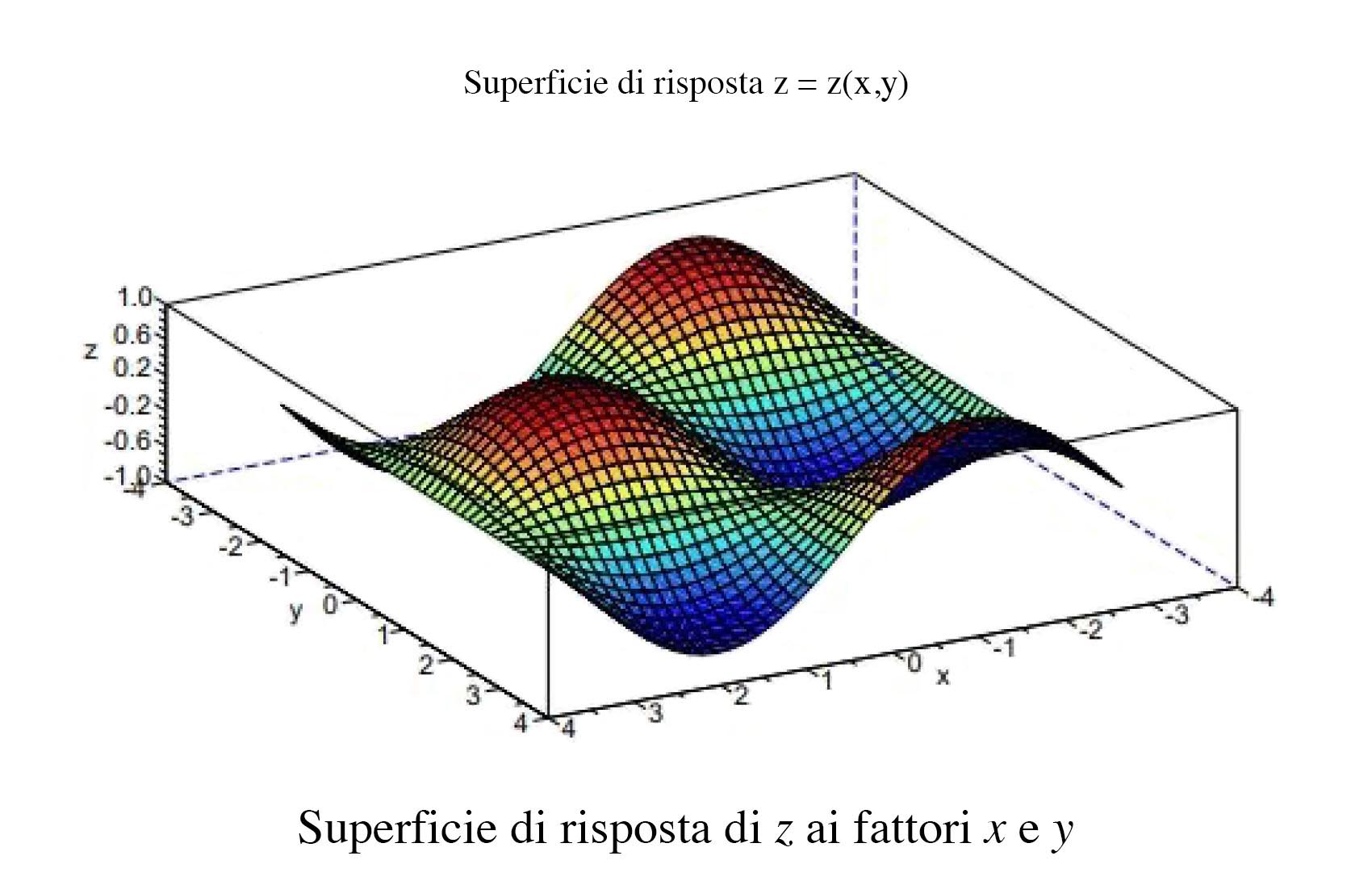
Quindi l’analisi DOE simulata è esaustiva?…NO.
L’analisi DOE ‘virtuale’ è un aiuto importantissimo nella fase progettuale per decidere che strada intraprendere e che scelte progettuali fare.
L’analisi DOE del processo HPDC andrebbe invece sempre condotta in fase di campionatura e testing dello stampo.
In un mondo ideale dovremmo avere, dopo la campionatura, la formulazione di quella funzione n-dimensionale che ci permette di capire e predire (entro certi limiti) il comportamento del nostro stampo in funzione della variabilità delle grandezze in input del processo.
Ricordiamoci però che il processo reale è molto più complesso della simulazione.
L’obiettivo è ottimizzare il processo reale. Anche il modello fisico più raffinato è una approssimazione della realtà, con un preciso intervallo di validità.
La reale validazione di un progetto perciò è sempre fatta sul campo.
E’ quello che, più o meno inconsciamente, fa un buon tecnico di fonderia quando varia i parametri di stampaggio per ottimizzare la resa dello stampo.
Il metodo DOE è la “cassetta degli attrezzi” che fa la differenza!
In breve (non me ne vogliano i teorici!) la tecnica DOE è molto simile: si analizza la risposta del sistema in modo sistematico e metodico, con una teoria statistica alla base volta ad ottimizzare il numero di esperimenti e l’interpretazione dei risultati.
Utilizzare anche solo parzialmente questa “cassetta degli attrezzi” statistica per comprendere meglio il comportamento dello stampo può fare la differenza nelle ottimizzazioni post campionatura di una nuova attrezzatura.